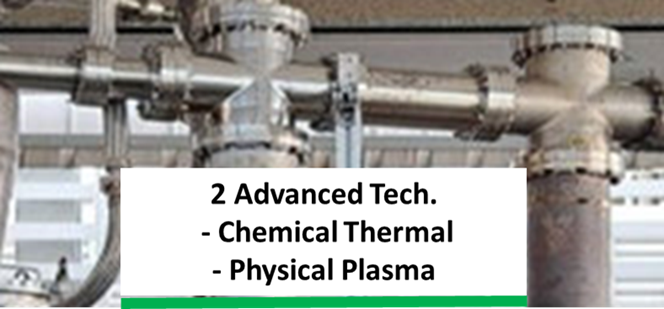
SMR is a process where traditional chemical plants use methane to produce hydrogen for decades.
Although Water electrolysis to produce hydrogen consumes a lot of electricity, it is a green hydrogen manufacturing solution that has been well known and installed in in recent years.
Ours: Thermal cracking of methane to produce hydrogen is the most innovative process. Our innovative two process on thermal cracking tech. allow methane to produce green hydrogen and carbon black at the same time, with no carbon emissions and relatively low power consumption. They are proven to be suitable for quantitative production in different scale scenarios under full-time operation
Tradition- Steam Methane Reforming (SMR)
While hydrogen is thought to be a major player in the clean energy of tomorrow, SMR is a very polluting process widely used by almost all chemical plants till today. SMR uses natural gas and water as a feedstock, and more than 10 kg of CO2 are liberated in the atmosphere with each kg of H2 produced.
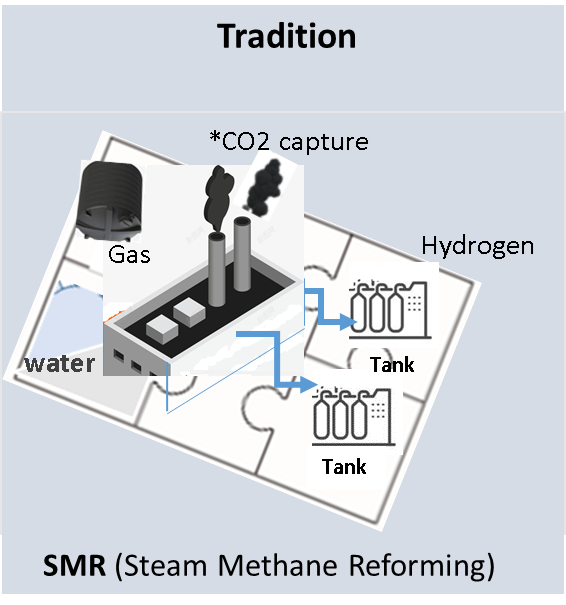
High Energy consumption method
The most know clean alternative to SMR today is water electrolysis. This process uses water and electricity as feedstock and produces hydrogen and oxygen for zero carbon emission. While the produced H2 is clean, the water electrolysis technology is an expensive process which needs lots of electricity during production. The cost of each kg of H2 produced using this process can be couple times more expensive than SMR.
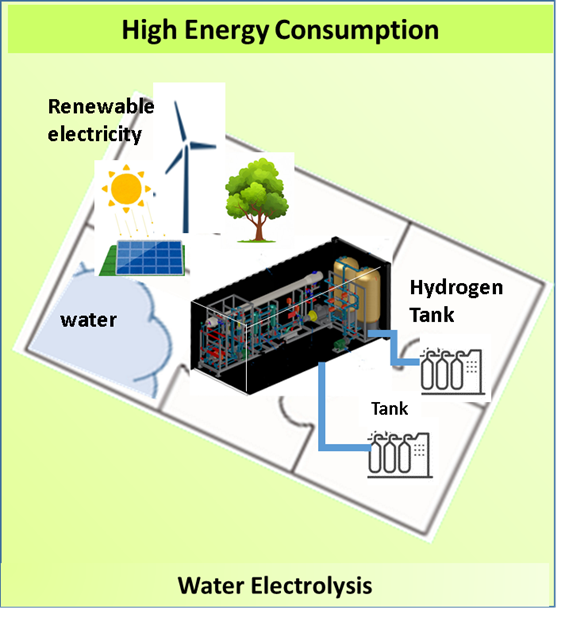
Ours: Low Energy consumption method
Our technology is a pyrolysis process of uses bio methane (biogas or natural gas) and much less electricity (accepts any renewable electricity) as feedstock. On the contrary of SMR, Plasma/ Physical Pyrolysis does not produce any CO2 because it uses the clean heat generated by our physical plasma to crack the methane molecule (CH4) into hydrogen and solid carbon powder (a by-product with high purity and value on the market) for zero carbon emission. Plasma / Pyrolysis uses also electricity, similarly to water electrolysis. But, Plasma / Pyrolysis uses 5 times less electricity than electrolysis and making the operational costs more than 50% cheaper than electrolysis, while competitive to the tradition cheap operational costs of SMR.
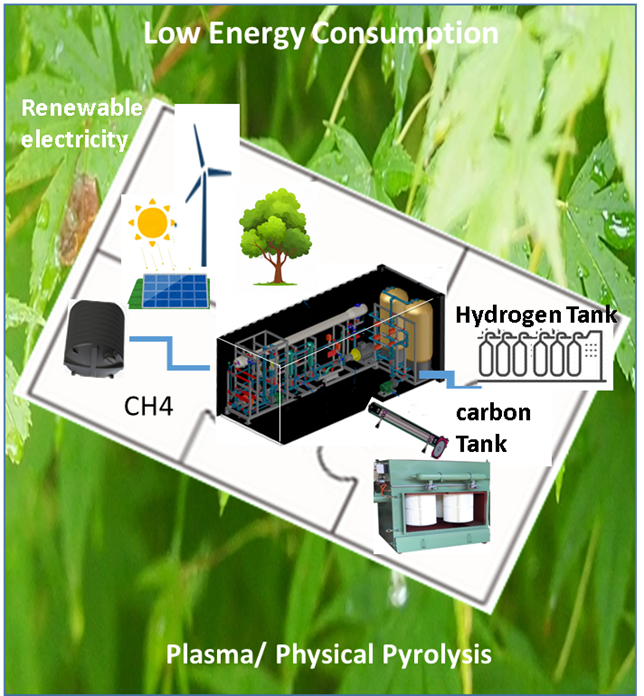

Overall, natural gas power plants with large power generation capacity face huge pressure to reduce carbon emissions. The turbine gas generator of this power plant can mix green hydrogen with methane and burn it together to generate electricity (their mixing ratio can be gradually increased from 10-15% or more), which can immediately produce a very considerable carbon reduction effect. Similarly, the pressure of installing carbon capture system (CCS) in the hydrogen production system of chemical plants is also very high.
As for other small and medium-sized hydrogen production applications, such as the semiconductor industry and the hydrogenation needs of transportation vehicles, the scale of thermal cracking hydrogen production is relatively small and easy to configure in modules.
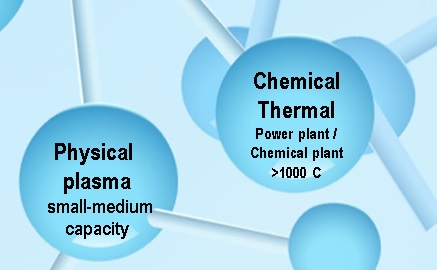
Yes. We proved in operating of two thermal cracking technologies. Both of them can directly crack natural petrochemical gases (methane, CH4) or renewable energy (Biogas) into clean green hydrogen and high-purity carbon black without any carbon emissions.
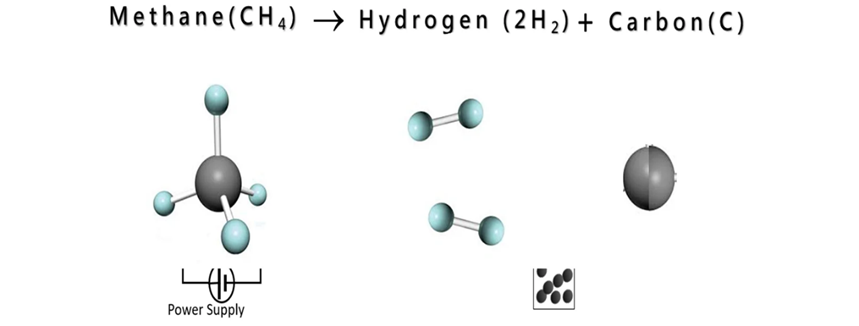
Methane Pyrolysis: Cracking CH4 to Green H2 and solid Carbon Black
A: Chemical Thermal Pyrolysis System
A proved high-temperature massive hydrogen production plant with hydrogen and carbon black production rates > 60 Kg/h and 180 Kg/h. System capacity of the clean hydrogen can be expanded to up to 200-400 kg/h or larger.
The required temperature is above 1000 degrees Celsius, and the best thermal cracking efficiency can achieved for zero carbon emission.
B: Physical plasma pyrolysis system
This is a friendly, compact system that operates at room temperature. Its hydrogen and carbon black production rates are as high as 50 kg/h and 150 Kg/h respectively. Because the plasma injection and the pyrolysis reaction is controlled within a limited environmental space, and the surface of the furnace body can be touched by hand, thus providing a high degree of safety.
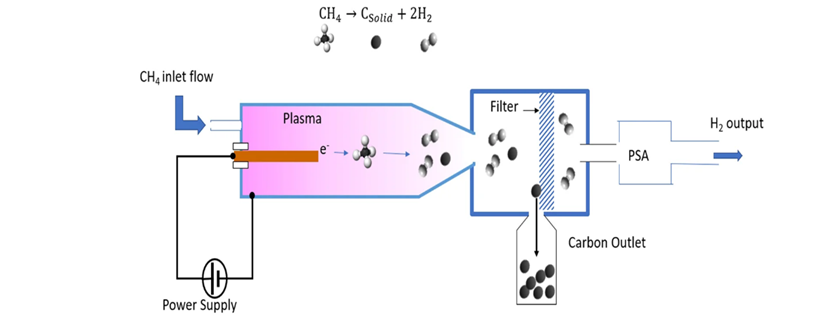
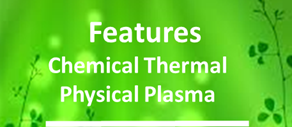
Energy Conversion
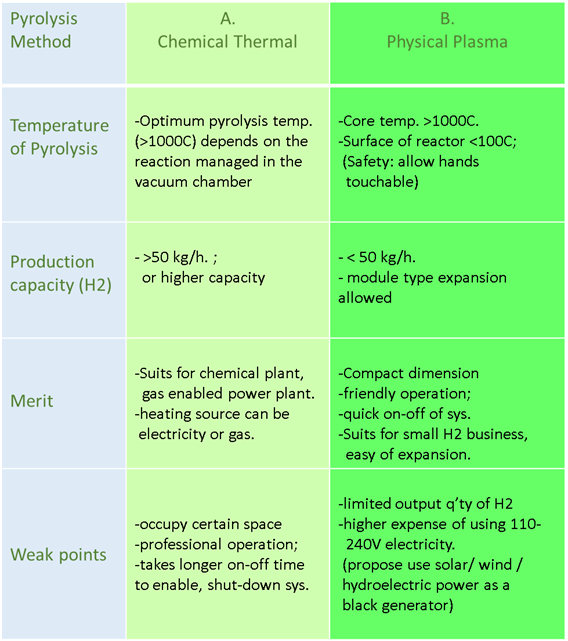
A. Chemical Thermal
Chemical thermal method is suitable for mixed nature gas (CH4) in gas power plants. The turbine generators can immediately achieve large carbon reduction effects.
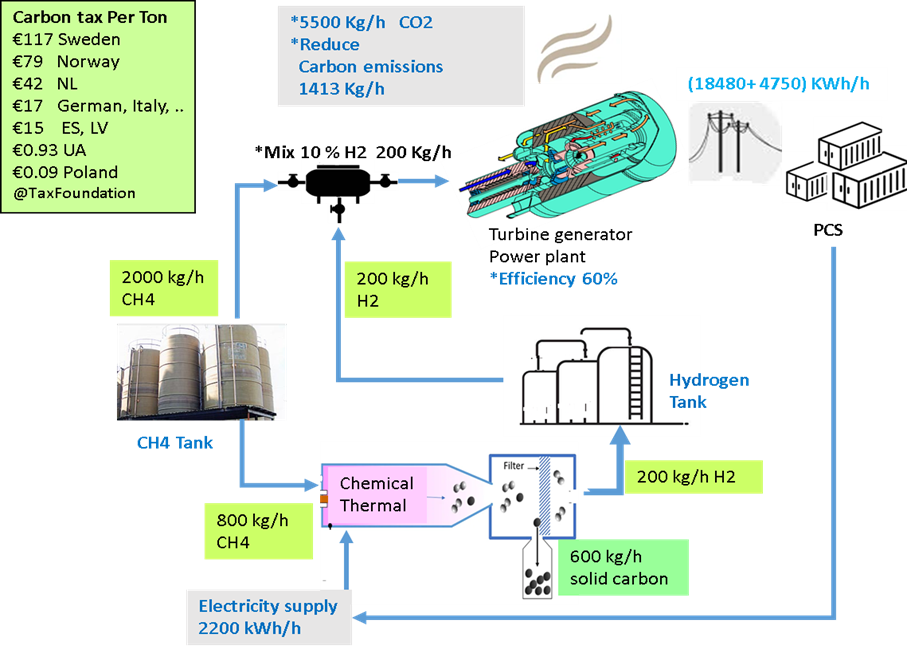
B. Physical Plasma
It takes 9 kWh electricity to get 1 kg/h hydrogen and 3 kg/h solid carbon when the inlet is 4 kg/h CH4 continuously. Users can install a system with a smaller capacity first (1-10 kg/h output of H2) and then expand the total hydrogen output multiple times (40-50 kg/h H2) according to demand. To save power consumption, it is recommended to use renewable energy to start the system and provide operating power.
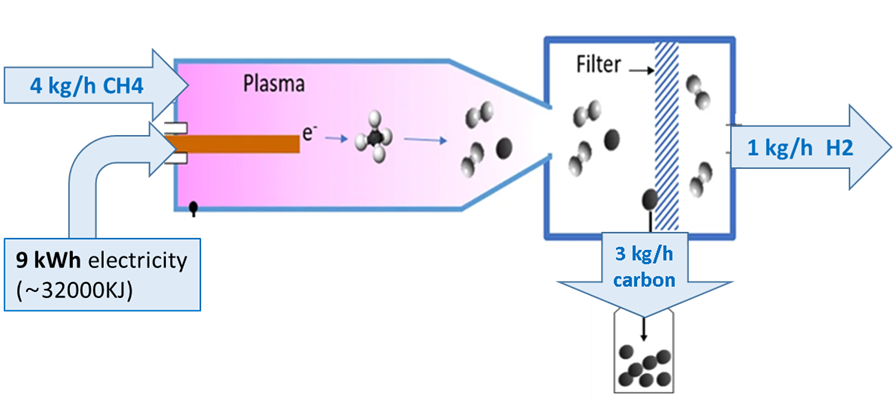
Experience
The technical team we work closely with has accumulated uninterrupted operational experience using these two thermal cracking methods at different production capacity scales over the past few years, directly assisting the world’s most commonly used natural gas power plants to mix hydrogen and burn them to significantly reduce carbon emissions. , also directly built a new thermal cracking carbon emission-free system for the hydrogen manufacturing plant, and also increased the solid carbon black by-product for users. Let us work together, make contribute to global energy conservation and emission reduction with innovative processes.
A. Chemical Thermal
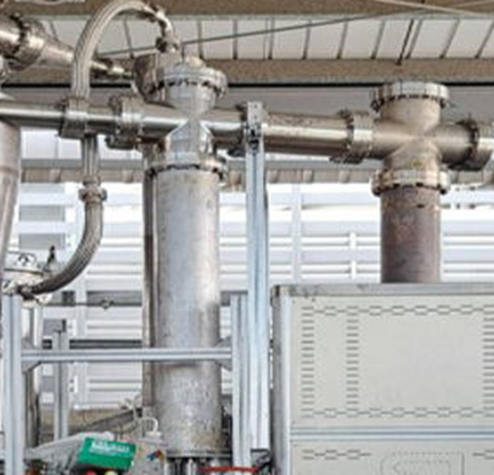
B. Physical Plasma
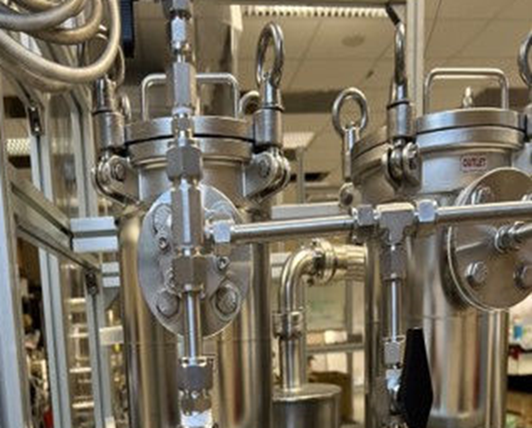
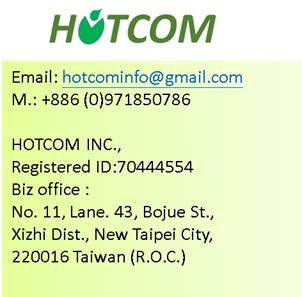