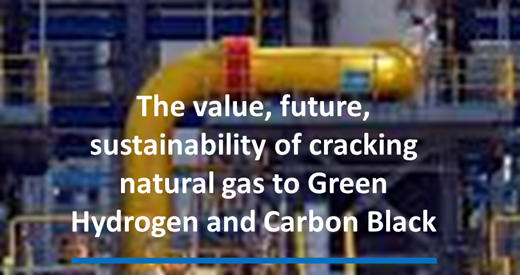
- This technology proves that methane (CH4) in natural gas can be directly and
efficiently cracked into hydrogen and carbon black. It is sufficient to meet the
continued growing market demand for hydrogen energy and carbon black in the future. - Hydrogen can be used in fuel cells, semiconductor, electronics, and hydrogen fuel cell based
vehicle, vessel, rail and many other industries. - Our solution can assist small and medium-sized enterprises in setting up private hydrogen power
generation system to provide green electricity, achieving ESG carbon reduction goals. - All of natural gas-based power plants can be directly converted into hydrogen power plants, solving the problem of carbon dioxide emissions without requiring import, transportation, or storage. And these chemical gas plants can easily upgrade to a carbon free, hydrogen manufacturing environment.
- The nano-scale carbon black powder can be used as a high-value industrial raw material in lithium batteries, tire manufacturing, the rubber industry, the semiconductor industry, and others.
This also means that the carbon black industry can not only use a more streamlined process to
produce high-quality carbon black but can also simultaneously involve in the manufacturing of green hydrogen for extra revenue.
Green Hydrogen Market Size Poised to Surge USD 165.84 Billion by 2033
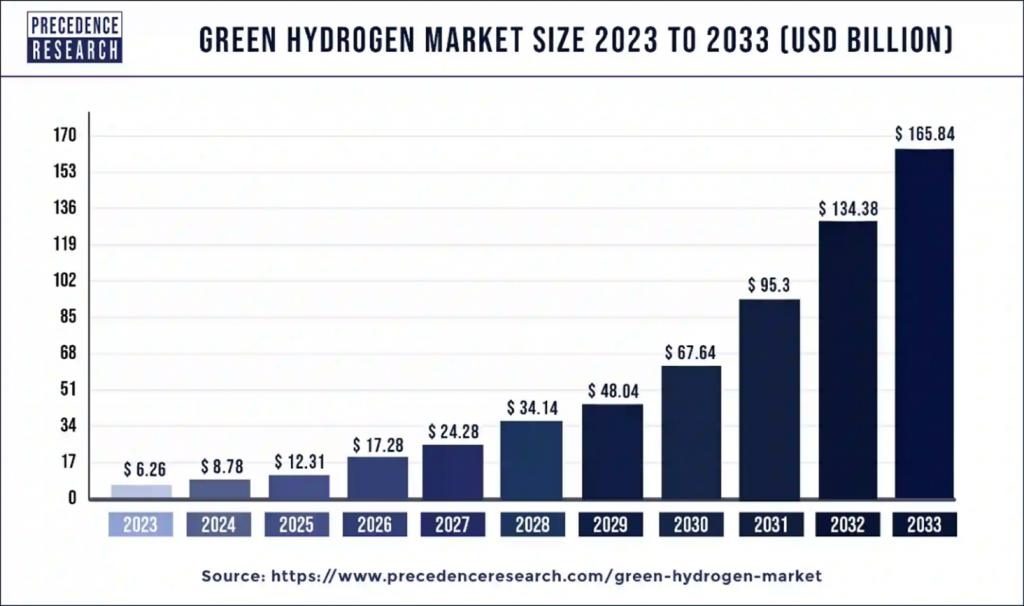
Cost comparison of Hydrogen production methods
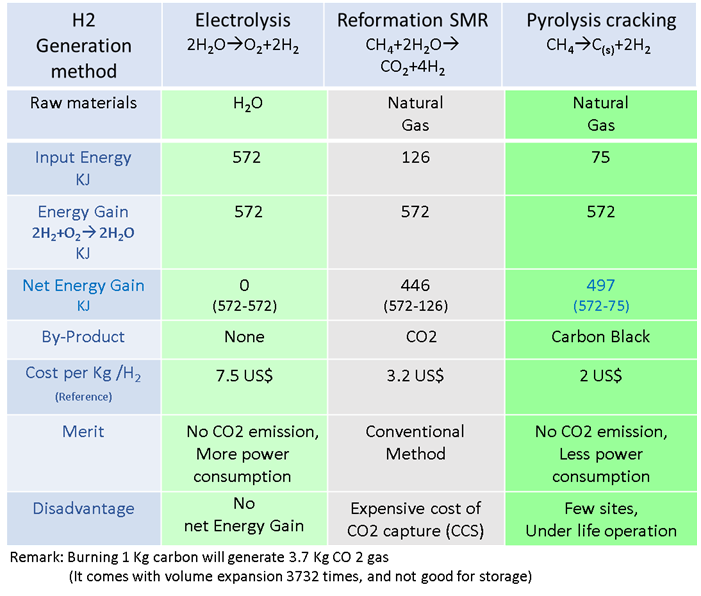
The Performance compared to the tradition CH4 power plant
(Based on the burning of 1-ton natural gas)
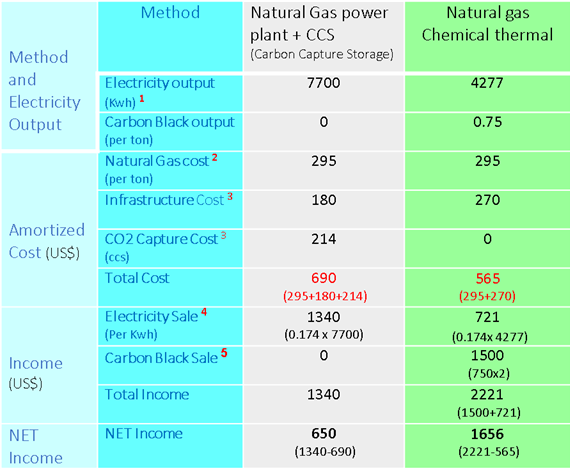
- Assume the efficiency of the Electricity power plant on 50%
- Gas cost: landing price of LNG quite unstable during the past years. We assume the average, fix price US$295 per ton. (1KL: 0.45T: 0.57m3)
- The cost on Infrastructure and CCS are a roughly number refer to the original investment on the fixed asset.
- We assume the whole sales price of electricity calculated by the same level on 0.174 US$ /Kwh even use different method.
*By the way, the saving of carbon tax is not include in the above calculation. - Carbon black price: We assume a lower grade of carbon black price on the market around US$2.0/Kg
New Art of making Nano-scale Carbon Black through Methane Pyrolysis
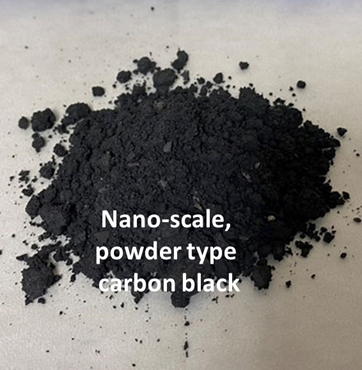
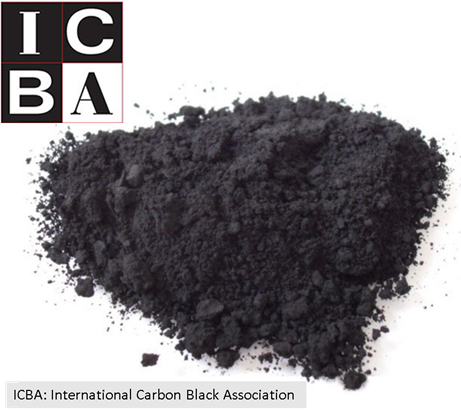
According to the description of ICBA
Carbon Black is produced using two carbon black manufacturing processes (furnace black and thermal black). These processes produce nearly all of the world’s carbon blacks, with the furnace black process being the most common.
(Following paragraphs are abbreviate from the web of ICBA)
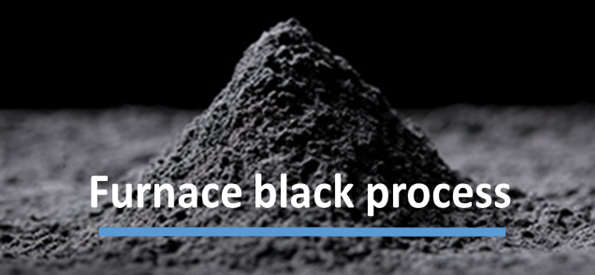
The furnace black process uses heavy aromatic oils as feedstock. The production furnace uses a closed reactor to atomize the feedstock oil under carefully controlled conditions (primarily temperature and pressure).
The primary feedstock is introduced into a hot gas stream (achieved by burning a secondary feedstock, e.g., natural gas or oil) where it vaporizes and then pyrolyzes in the vapor phase to form microscopic carbon particles.
In most furnace reactors, the reaction rate is controlled by steam or water sprays. The carbon black produced is conveyed through the reactor, cooled, and collected in bag filters in a continuous process. Residual gas, or tail gas, from a furnace reactor includes a variety of gases such as carbon monoxide and hydrogen. Most furnace black plants use a portion of this residual gas to produce heat, steam, or electric power.
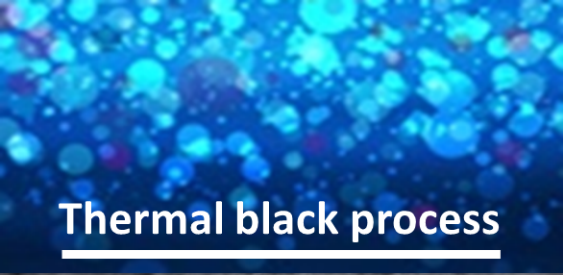
The thermal black process uses natural gas, consisting primarily of methane or heavy aromatic oils, as feedstock material. The process uses a pair of furnaces that alternate approximately every five minutes between preheating and carbon black production.
The natural gas is injected into the hot refractory lined furnace, and, in the absence of air, the heat from the refractory material decomposes the natural gas into carbon black and hydrogen. The aerosol material stream is quenched with water sprays and filtered in a bag house. The exiting carbon black may be further processed to remove impurities, pelletized, screened, and then packaged for shipment. The hydrogen off- gas is burned in air to preheat the second furnace.
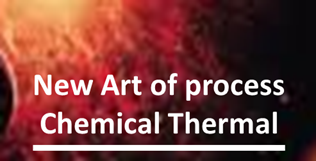
Refer to the thermal black process, our solution on Chemical Thermal technology adopts a quite simpler
and lower energy consumption process, and also passes natural gas through a high-temperature managed chamber.
Directly crack CH4 into Nano-scale carbon black powder and clean green hydrogen with high energy
value. Our solution is a next generation technology to produce carbon black and no need these complicated facilities on steam, water, off-gas processing and others.
Whether the quality of green hydrogen that is better than 99.9% after purification, or carbon black with extremely high purity after gravity selection of impurities, No CO2 emissions
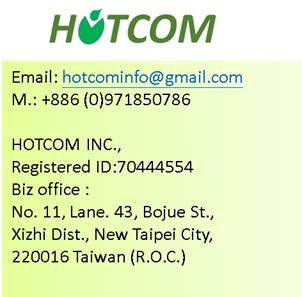